Two students from the Manufacturing Engineering Technology - Welding & Robotics program worked with industry partner CAMufacturing Solutions Inc. to produce completely enclosed 3-D cubes using the innovative wire-arc additive manufacturing (WAAM) process.
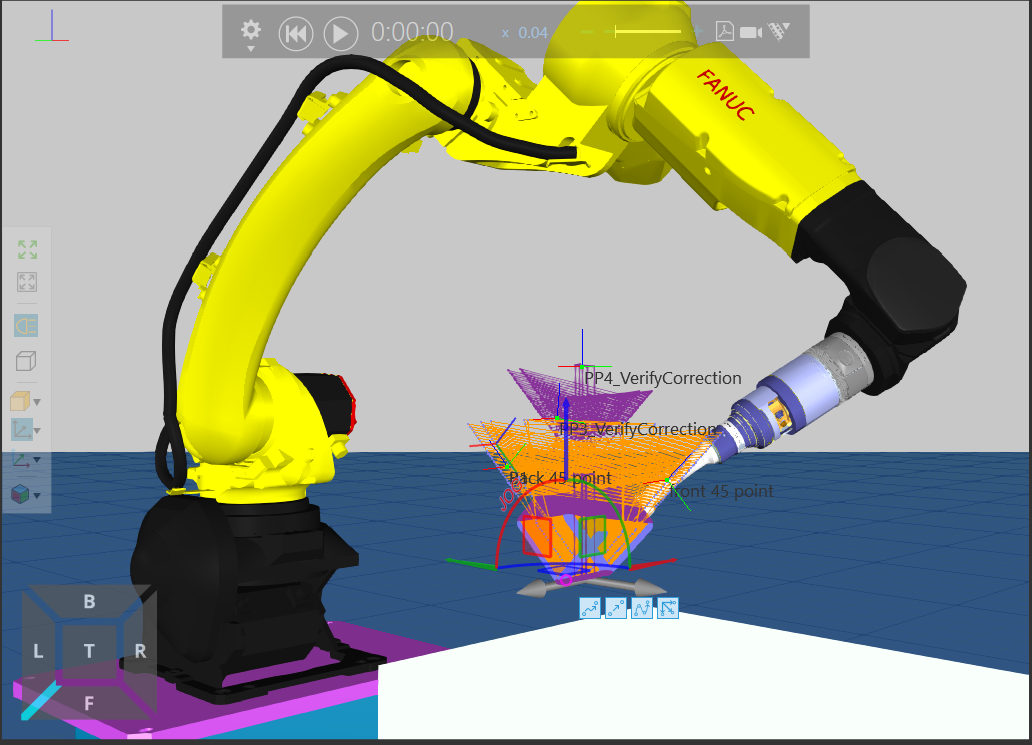
Two students from the Manufacturing Engineering Technology - Welding & Robotics program worked with an industry partner to produce completely enclosed 3-D cubes using the innovative wire-arc additive manufacturing (WAAM) process.
Jackson Macor and Scott McElhone, under the guidance of Joe Barnes and other faculty, worked closely with CAMufacturing on their capstone project to produce the hollow cubes as well as other interesting shapes like a boat propeller or useful industrial components such as a hollow wide-flange beam.
The pair focused on creating thin-walled structures with the WAAM process. McElhone explained: “This is where you get a robot to weld directly onto its previous weld, building up a structure just like a plastic 3-D printer but much stronger.”
They started by creating a 3-D model of a part, taking that file into computer-aided manufacturing software (Mastercam) and using CAMufacturing’s slicing software to cut the shape into many thin layers to create individual toolpaths for each weld. This file was then taken to offline robotic programming software (Octopuz), where they simulated the part being welded and fine-tuned the toolpaths.
Finally, the file was sent to one of Conestoga’s welding robots to print the structure.
“The project was so much fun, learning and experimenting the whole way. But we faced many challenges, from learning new software to hardware issues. It was extremely satisfying when we saw our first part completed by the robot, and that added more fuel to the fire to keep pushing the limits and creating more,” McElhone said. “In the end, the project was a complete success, and I am very proud of myself for what my partner and I were able to achieve.”
Barnes, faculty and program coordinator, applauded the students’ success at printing the metal cube. “The premise was to prove that an enclosed hollow structure, printed in situ, could be achieved through the manipulation of programming software to create the tool path for the robotic system,” Barnes said. “This project proves that with advanced programming techniques and software, coupled with fine-tuned welding processes and parameters, it is possible to use the process to produce complex components in various positions.”
One of the unique aspects - and the most challenging problem to overcome - was printing with this process without manipulation of the part.
Barnes said the pair had to overcome multiple issues with the welding process itself. That included making it cool enough to hold in place without “dripping,” particularly on the cube’s edges that were printed at a 45-degree angle to the worktable, and also manipulating the software settings to orient the welding torch to deposit the liquid weld metal perpendicular to the growth of the part.
Conestoga's work on WAAM continues to evolve as students explore this innovative method through a range of applied research projects. The WAAM process combines arc welding, industrial robotics and programming to transform a welding robot into a large-scale 3-D printer of metal shapes.
The possibilities excite McElhone.
“Wire-arc additive manufacturing is still in its infancy as a manufacturing process, and I am very proud to be a part of it since the beginning and I cannot wait to see where it goes from here at both Conestoga College and worldwide!”
The project was supported by Conestoga's Smart Manufacturing & Advanced Recycling Technologies (SMART) Centre, which was established in 2020 to support applied research, technical services and training in the areas of advanced manufacturing, advanced recycling technologies, and cyber security. The centre is part of Canada's 60 NSERC-funded Technology Access Centres, a network of state-of-the-art applied research and innovation centres spanning the country.
The three-year advanced diploma in Manufacturing Engineering Technology - Welding & Robotics offers hands-on learning in a state-of-the-art facility where students learn about operating and troubleshooting automated and robotic welding systems. This program combines theoretical knowledge with applied skills in the control of robotic and automated equipment using electronics, programmable automation controllers, computers, hydraulics, and pneumatics.
The program is part of Conestoga’s School of Engineering & Technology, which offers a comprehensive suite of engineering and technology programs with a wide range of credentials.