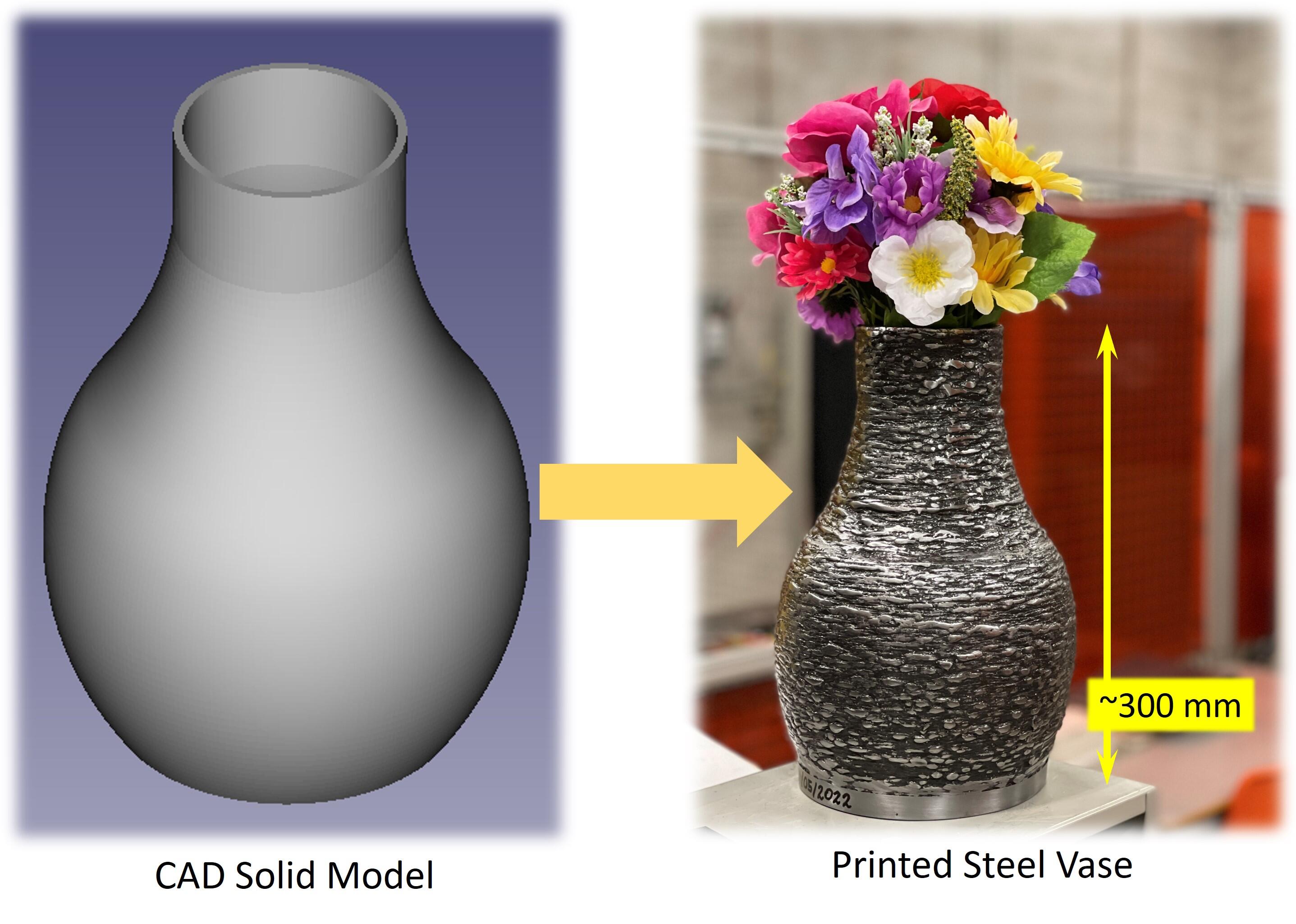
Recent graduates from Conestoga’s Manufacturing Engineering Technology - Welding & Robotics program had their capstone project highlighted in a national technical journal.
Kevin Liu and Farid Shigapov, under the guidance of professor Tam Nguyen and other faculty, demonstrated a new method of using Canadian-developed software to convert an object created using computer modelling into a large steel component, printed on one of the college’s arc welding robots.
The steel components were produced at the Cambridge - Fountain Street campus using specialized methods developed by the School of Engineering & Technology called wire-arc additive manufacturing (WAAM).
Combining conventional industrial welding robots with 3-D printing offers a unique opportunity to create large, complex metal structures in a cost-effective and efficient way, Shigapov said.
But achieving that was challenging. Starting from scratch, the students had to figure out every step to produce a part and the programming was especially challenging because industrial welding robots typically perform repetitive tasks.
“WAAM, however, requires generating complex toolpaths to create the desired 3-D geometry which, in our case, took three different pieces of software to achieve. It was very time-consuming and required us to develop specialized knowledge in offline robot programming. Once we established the sequence and worked out all details, the rest was easy - watching the robot print.”
Having the opportunity to participate in applied research while a student at Conestoga was “incredibly rewarding,” Shigapov said. “It allowed me to bridge the gap between theoretical knowledge and real-world applications. Witnessing the potential of WAAM firsthand and contributing to its development was an inspiring experience.”
This method can produce metal objects on a much larger scale than currently possible with laser-based systems and also offers several other advantages around production cost, operational safety, and improved material quality as detailed in the article.
CAD-to-Print Integration for Wire Arc-Additive Manufacturing was published in the spring 2024 edition of the Canadian WELD journal.
Conestoga's work on WAAM continues to evolve as students explore new materials such as high-strength low-alloy steels, hollow thin-walled steel components, and aluminum-alloy objects printed with this innovative method.
The paper concludes: “Two full-scale products were printed in steel to demonstrate the capability, and documentation was created to facilitate future work at Conestoga College as they continue to unlock the potential of the WAAM process.”
Jim Galloway, professor and welding program coordinator, said the faculty are very impressed by the high-quality of work and level of enthusiasm shown by Liu and Shigapov on the project that advances the college’s work on this new technology.
“Conestoga is beginning to explore new opportunities for this revolutionary technology, the products that can be made by it, and the superb properties of the materials printed by the WAAM process.”
Conestoga’s three-year advanced diploma in Manufacturing Engineering Technology - Welding and Robotics combines theoretical knowledge with applied skills in the control of robotic and automated equipment using electronics, programmable automation controllers, computers, hydraulics and pneumatics. Emphasis is placed on effective techniques for designing, modifying, installing, testing, maintaining, repairing, and troubleshooting equipment and systems.