Conestoga researcher Dr. Hamid Karbasi was among a select group of experts invited to Yale University to share details of his research into the use of artificial intelligence (AI) and machine learning to improve recycling processes.
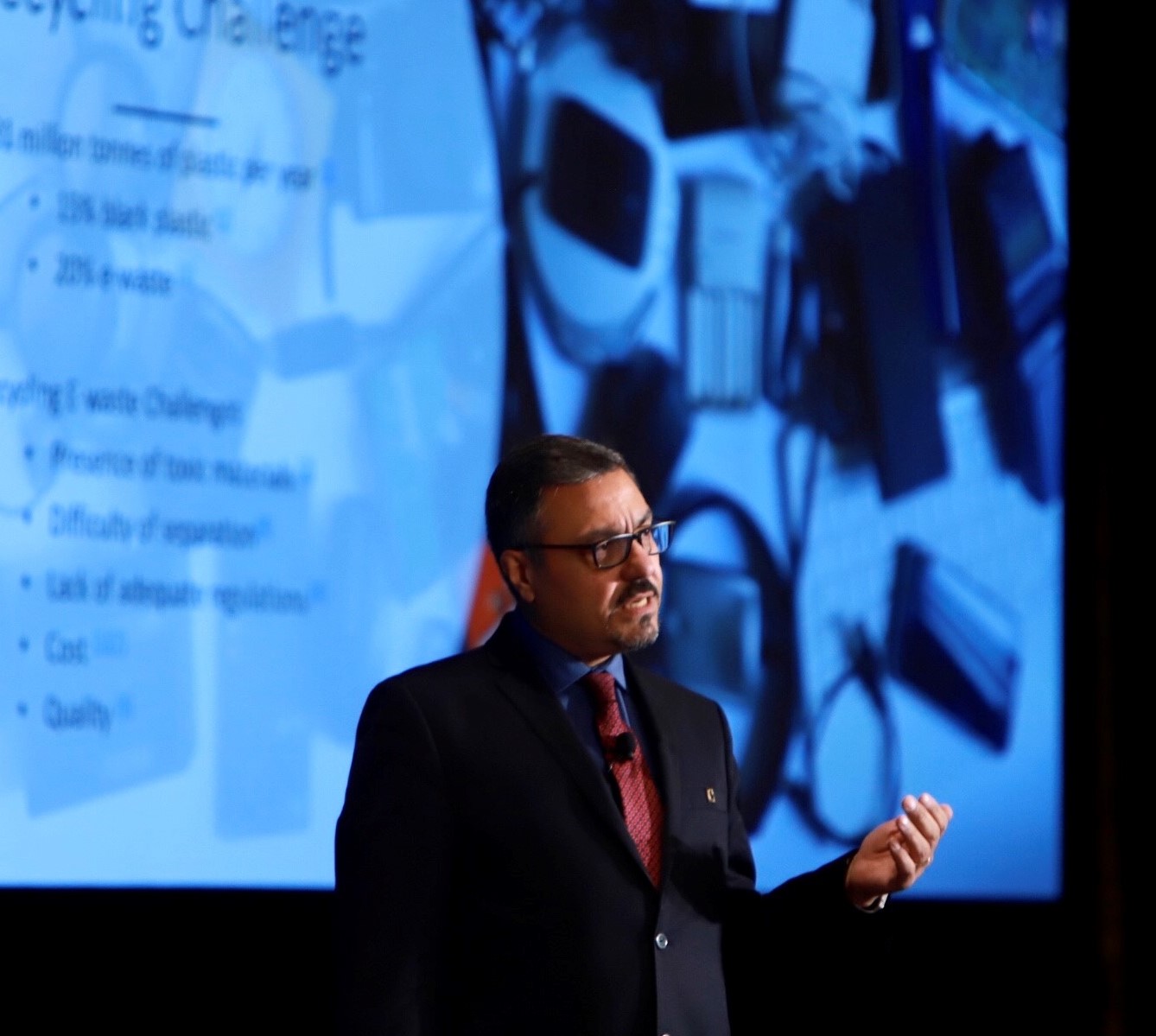
Conestoga researcher Hamid Karbasi recently presented at the 2020 Plastics Recycling Conference and Trade Show in Nashville, Tennessee where he discussed his research into solving the challenges posed by black plastics. Photo credit: Brian Adams Photo for Resource Recycling Inc.
The Future of Recycling at the Human-Robot Interface Workshop took place in New Haven, Connecticut February 17 and 18 and brought together more than two dozen researchers and industry leaders to discuss current recycling technologies and the best approach to adopting robotics in waste management.
“People are realizing that robotics and automation are gaining traction as a way to improve recycling practices,” said Karbasi. “Right now, the industry relies on human operators to receive, sort and separate materials. It’s a costly and inefficient process.”
According to Karbasi, ensuring purity is increasingly important for materials recovery facilities (MRFs), which operate on narrow margins and are vulnerable to fluctuating commodity prices.
As Conestoga’s NSERC Industrial Research Chair for Colleges in Advanced Recycling Technologies for Waste Electrical and Electronic Equipment (WEEE), much of Karbasi’s research has involved working with faculty, students and industry partners to explore technology solutions and products that can be adopted by recyclers to increase resource recovery and reduce the amount of e-waste going to landfills.
“These facilities must separate materials like copper, aluminum, plastics and glass so they can be sold and re-manufactured into new products. If there’s any contamination, these materials lose their value. Robotic technology, using image processing and AI capabilities, can address that challenge.”
During his presentation at Yale, Karbasi shared his vision for the future of the recycling industry. That vision includes the development and adoption of robotic lines, much like the ones used by the car manufacturing industry.
“You can put a team of robots on a line, assign different tasks and then pull out material in a very efficient way,” explained Karbasi, who is overseeing the development of a Next-Gen Electronic Waste Recovery Pilot Plant at Conestoga’s applied research facility in Cambridge.
Once completed, the pilot plant will use AI and machine learning technologies to develop new solutions for dismantling electronics, removing plastics and recovering valuable materials. WEEE is the fastest growing sector of solid waste with 40 to 50 million tonnes produced globally each year. Only 15 to 20 per cent of it gets recycled responsibly.
“This is an area where we can develop technology for good. To keep our planet livable and protect our resources. There is huge merit here,” said Karbasi.
One day after speaking at Yale, Karbasi attended the 2020 Plastics Recycling Conference and Trade Show in Nashville, Tennessee - an annual event that brings together 2,000 plastics recycling experts to discuss the latest innovations and challenges facing the industry.
Here, Karbasi took part in a panel discussion focused on plastics recycling and his research into solving the challenges posed by black plastics.
“Sorting plastics by polymer composition is an enormous issue for the recycling industry, especially black plastics,” said Karbasi. “Current technologies rely on the use of reflective light, but black plastics absorb light and therefore can’t be identified as easily.”
Karbasi’s research includes developing a terahertz-based sorting system that works like an x-ray but is safer to be around and more cost effective for recyclers to implement. The terahertz system eliminates reflection issues, making it easier to identify and isolate black plastics.
According to Karbasi, his research team was able to achieve a more than 90 per cent purity rate when sorting black plastics. The system, developed through an applied research project with an industry partner, is also capable of operating at the speed needed for a large-scale industrial operation.
“Mixed plastics are of no use to the recycling industry,” explained Karbasi. “But once you sort them by polymer type, you are able to mix it with virgin material and use it to re-manufacture quality products. This type of research has the potential to revolutionize e-waste recycling.”
Conestoga Applied Research and Innovation brings together faculty expertise, student researchers and state-of-the-art technology to support specialized research in sectors of key economic growth. The college is ranked among Canada’s top 12 research colleges, supporting the needs of industry and community partners while providing students with opportunities to build real-world skills.
Over the past year, more than 3,600 students and close to 270 faculty and staff at Conestoga were engaged in applied research projects.